At a headline level, it was a mixed third quarter for firms in the construction supply chain. Construction product manufacturers reported a second quarter of growth in sales volumes, although for the heavy side, sales remained lower than a year earlier. Civil...
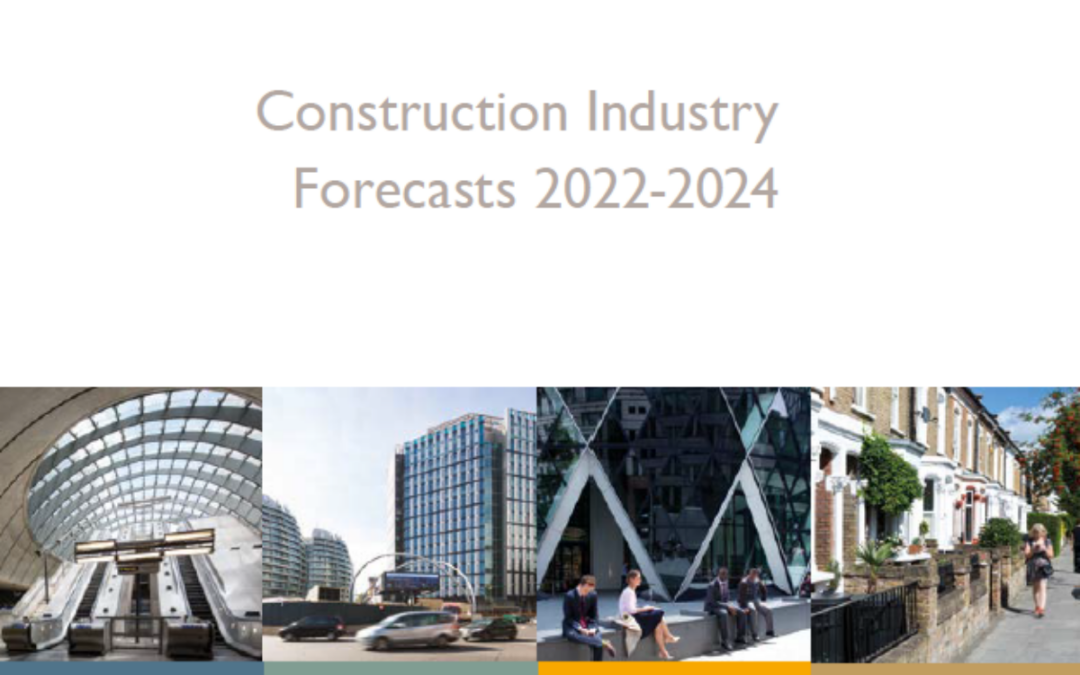
Construction activity buoyant, but strong headwinds coming, warns Construction Products Association
In its latest quarterly forecast, the Construction Products Association (CPA) sees a dramatic slowing in growth, with uncertainty ahead as global issues start to affect the UK market.
In previous years, the predicted 2.8% growth in construction output anticipated by the CPA team would be cause for celebration. However, while a robust figure, this is a sharp revision down from the 4.3% growth forecast just three months ago.
Demand remains strong across the industry in Q2, and the current project pipeline suggests that this will support activity levels until at least 2022 Q3. The downward revision to the growth forecast stems from concern around a host of price pressures arising from both local and global issues.
Prior to the conflict in Ukraine, UK construction was already facing labour and product availability issues and the impact of reverse charge VAT and IR35. Rising energy costs were driving near-record price increases in construction products and the continued conflict is exacerbating this issue.
The impact of these pressures, and of more general rising costs, on demand will vary considerably by sector. Across the board the picture is one of positive market conditions in the short term with anticipation of tougher times ahead.
In private housing repair, maintenance and improvement, the stellar performer post the initial Covid-19 lockdowns, SMEs report that demand remains high, but this is the sector arguably most exposed to current price inflation, falls in consumer confidence and pressures on household incomes. Overall, output is expected to fall by 3% in 2022 and 4% next year from current all-time highs.
Private housing, the largest construction sector, remains strong, with housebuilders reporting resilient demand. Longer term, there must be questions over consumer confidence but output in this sector is forecast to rise by 1% in both 2022 and 2023. This contrasts with the 3% per year growth forecast three months ago.
The fastest growth is expected in the industrial sector, in which output is forecast to rise by 9.8% in 2022 and 9.3% in 2023, due to a strong pipeline of warehouse projects, resulting from a long-term shift towards online shopping.
Infrastructure, traditionally less affected by immediate economic conditions, remains positive. Large projects such as HS2, Thames Tideway and Hinkley Point C combined with the five-year spending plans in Page 2 of 3 regulated sectors such as rail, road and power generation point to a forecasted growth of 8.8% in 2022 and 4.6% in 2023.
On the supply side, the main immediate impact of the war in Ukraine for construction products will be the knock-on from rising energy prices and commodity shortages. Soaring energy costs will have to be passed on and lead to sharp rises in the cost of energy-intensive products. This will affect both imported products such as aluminium and steel and locally sourced products such as bricks and cement.
Contractors are likely to feel the pressure first, particularly those working to fixed-price contracts. For future projects, contractors will be forced to re-price, add fluctuation costs and introduce risk-sharing arrangements to deal with the uncertainty over potential cost inflation.
Noble Francis, CPA Economics Director, offered this summary of the latest figures:
“The major challenge is creeping uncertainty. The immediate picture is one of resilient demand and healthy pipelines. Longer term, the current inflationary pressures, if sustained, will have an increasingly depressing impact, while the continuation, or potential escalation, of conflict in Europe presents an existential risk.
“Specialist sub-contractors are feeling the effects first, particularly those working to fixed-price contracts. For future projects, contractors will be forced to re-price, add fluctuation clauses and introduce risk[1]sharing arrangement to deal with the uncertainty over potential cost inflation.”
Access the full report
FIS members have free access to the CPA Forecast and can download their copy via the button below.
Not a member? Contact FIS on 0121 707 0077 for details on joining.
See more news likes this
CPA Trade Survey reports mixed third quarter for firms in the construction supply chain
OPSS survey on Bespoke construction products
The Office for Product Safety & Standards (OPSS) has commissioned the Centre for Strategy & Evaluation Services (CSES) to conduct a study to develop its evidence base on "bespoke" construction products. This research will review current practices regarding the...
The Responsible No: New guidance – don’t risk it all on an amended contract
Establishing clear contractual arrangements from the outset of any construction project is critical. This is a core conclusion from virtually every review of the construction sector. As far back as 1866, The General Builders Association put out the following...